Construction Nightmares: How to Avoid and Handle Common Issues
Learn how to prevent, identify, and handle common mistakes like poor planning, communication issues, and low-quality materials.

In the Construction arena, every project no matter how big or small, has its own set of difficulties and achievements. No matter what project type you do, be it residential construction, commercial development, or even demolition or reconstruction, you better be mindful about not making common mistakes; otherwise you'll go over budget and timeline.
With the number of accidents that take place in construction areas, we can clearly imagine that this has both a health and safety impact on the workers who are involved. The fatal mistake, meaning following the recommended best practice, but still living in the conditions of risk and unpredictability, is the most common reason for safety problems at such worksites.
Yet, construction projects can have some obstructions, and despite that, when you hire the best talents in the construction industry, there will be situations when unexpected problems come up.
Beautiful design can evolve your current residence into a fantastic place to live, while bad architecture can quickly turn your dream home into a nightmare. But don't panic. Here, we guide you through the most common construction mistakes and offer practical advice on how to solve them.
Common Construction mistakes to avoid:
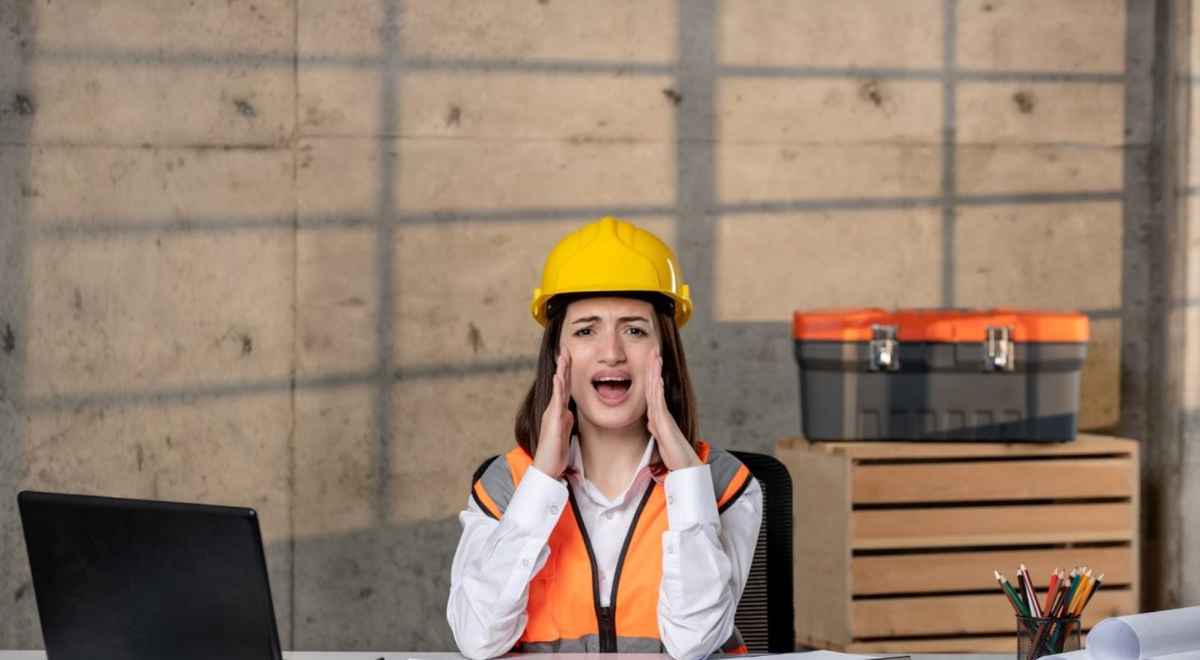
Avoiding mistakes during construction is important to ensure the safety, quality, and durability of any building or structure. Common mistakes to watch out for are:
- Improper planning and design:
Any flaw in content and design will cause a lot of trouble for later implementation. Hence, the plan of the entire project should have the details of all the aspects of the project, like structural integrity, performance and meeting government regulations.
- Ignoring the Rules & Regulations and Building Code:
Ensuring the dependability of structures is the core function of the building codes and regulations that regulate their development. Not adhering to such regulations can bring about serious complications that lead to financial losses, delays, or final results that can be dangerous for the demolition or reconstruction of some parts of the building.
- Lack of communication:
Shared responsibility and good communication between all parties involved in construction such as manufacturers, construction workers like builders, engineers, and general contractors, is a must. The foreboding factor is a mistake that may bring about an error, delay, or a high cost.
- Low-quality materials:
Using low-quality materials for some elements of the structure undermines the structure’s performance and the building's lifetime. The quality and safety of your home depend on the quality of the materials used in construction which either should be new or must conform to industry standards and if not, it will be a waste of money in addition to safety risks.
- Inadequate Site Prep:
The lack of proper citing in construction can deliver adverse effects like soil erosion, drainage, and instability. Site preparation such as leveling, drainage, and soil testing is crucial to perform the work right.
- Ignoring safety precautions:
On construction sites, production security is always on top. Refusal to apply the correct procedures would possibly result in a fatal accident or an injury. People must undergo proper training and all safety rules should be very well observed.
- Ignorance of environmental considerations:
The output of construction projects can be polluted because of the negative ecological influence that is in the form of air and water pollution. Environmental issues overlooked can entail compliance concerns, public dissent, and irreparable damage to the environment.
- Over-estimating time and budget:
Construction tasks can be buffered by other issues, but budget and time reduction is imperative and thus the project must have validity. Decrease costs, have better visibility for future business metrics, and do not panic when extreme situations occur.
- Poor quality control and inspection:
Quality control systems that are efficient, involving regular inspections and tests will have the potential to detect the problems at the early stages. Failing to process proper quality control procedures can have a high potential for errors, rework and the overall low quality of the results.
- Lack of proper documentation:
Documenting all construction procedures including contracts, agreements signing, drafting, and subsequent changes is an important aspect of good management of the project accountability. Failing to document improperly can bring disputes, and legal questions and can be a big challenge to maintaining and upgrading.
Best way to handle construction nightmare mistakes:
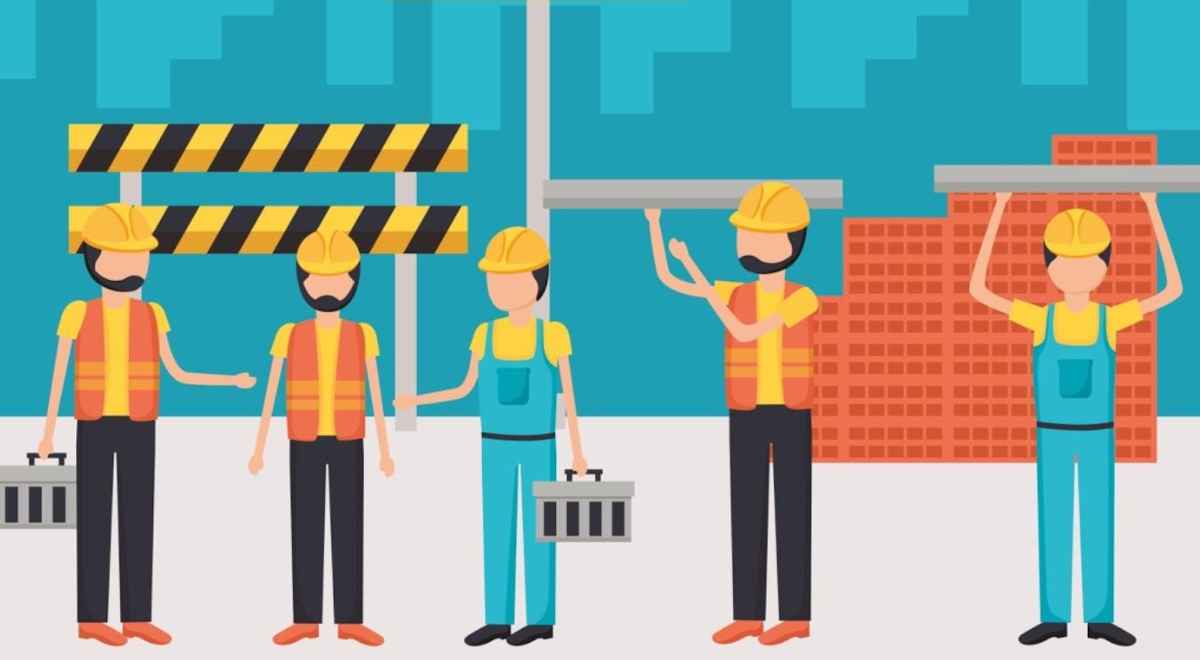
A good management of common construction defects can be considered a sure way of reducing the time spent on completing tasks, the overall expenditure, and the general project quality. Here are some mistakes as well as their correction and prevention:
- Rapid detection and open communication:
Immediately report the mistake to the ones who are in charge like the contractors and the project managers, architects, and engineers. Success in tackling problems and avoiding further challenges is very dependent on good communication and straightforward relationships.
- Assessment of impact:
Once a defect is identified it is crucial for the overall evaluation of its impact on the project on different dimensions in the form of schedule, cost, quality, and safety. After you realize the whole severity of the error, it will be easier for you to come up with the right decision that will be the best resolution to the challenge.
- Create a remediation plan:
Based on whether the error had a critical or merely procedural impact on the outcome, create a comprehensive remediation plan that stipulates the appropriate actions in mitigating the defect. The plan should contain timetables, employees’ roles, and procedures, as well as the current expenses and savings for the implementation of these changes.
- Expert consultation:
In some cases, putting skilled experts into the picture might be a prerequisite to getting the issue resolved, where designers, architects, or environmental consultants could possibly come in handy. Connecting with these experts can lead to getting meaningful details and guidelines for the specific situation which might be useful.
- Implementing Corrective Actions:
As soon as a plan of corrective actions has been set in motion, make sure to put those corrective measures in operation straight away. Hence, this may be performed by altering the way construction is conducted, the materials used, or the design of the product in order to identify the root of the problem and the means of its correction.
- Monitoring and Quality Control:
Monitor carefully during the procedure to make sure everything is operating as expected. Inspect the project on a regular interval, correct the defect; and ensure that the date of delivery given to the project meets the required standard and specifications.
- Documentation of Changes:
Be sure to maintain easy recordkeeping of the documents of all the construction defects, such as redrawn construction designs, specifications, changes, agreements, and correspondence with all the parties involved. The documentation of events is a crucial part of the whole project management, accountability, and legal issues.
- Managing Stakeholder Expectations:
Communicate with stakeholders throughout the remediation process, updating them on development status like variations in the plan of action, budget, or scope of the work. Maintaining trust in the project with accurate feedback on dates will position the company to address any unwarranted setback.
- Learn from mistakes:
When mistakes in the construction process are uncovered, it’s important to spend some time reflecting on the cause and learning lessons for the future. Use these for improving the processes, methods, and practice standards, to avoid such errors.
- Continuous Improvement:
Collect the data from the process of construction error handling and use it for the development of ongoing construction quality improvement measures. Exert the spirit of continuous improvement among the entire construction team; this way, lessons learned will be shared, and the best practices will be escalated to improve overall project performance.
Correct ways to avoid construction project issues:
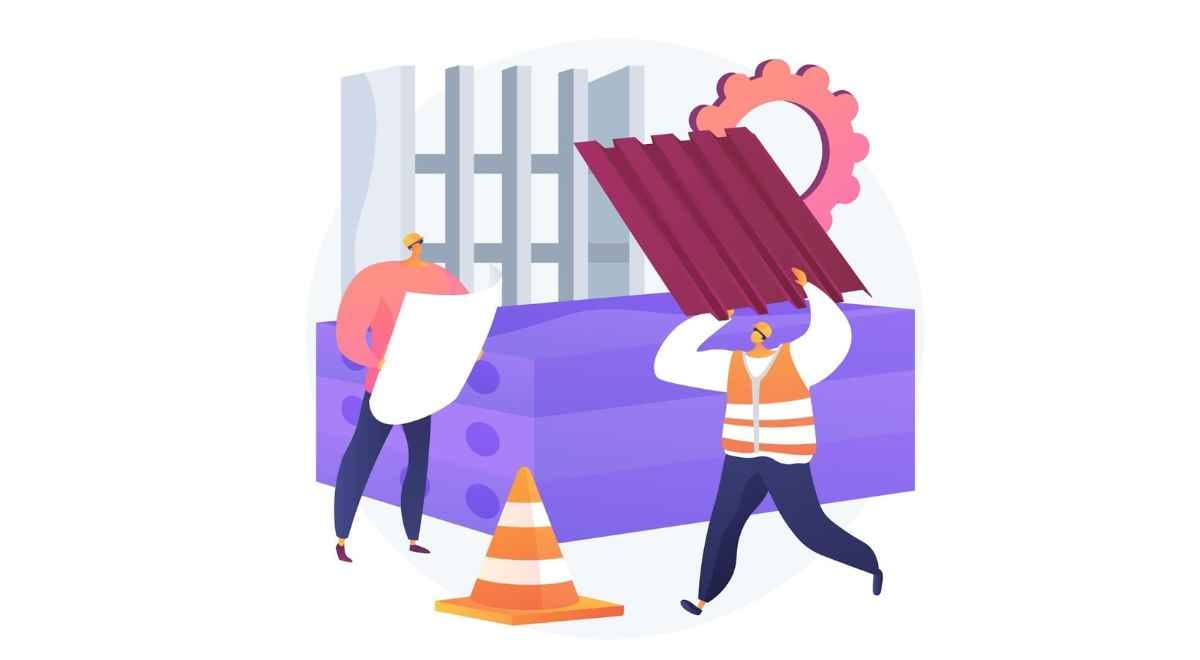
Abstaining with maintenance project issues is surely possible through proactive preparation, meaningful communication, coherent administration, and following the currently accepted standards throughout the course of the project. Here is an extensive aide on the best way to stay away from the most well-known development project issues:
Intensive Preparation and Plan:
- As specified by the planning and configuration stages, make adequate investments and let the requirements be clear and accurate in the processes.
- For instance, conduct in-depth site surveys, hazard investigations, and practicality assessments to identify issues earlier.
- Overall, create a competent team that will include engineers, architects, and any other specialists who would help in developing clear and exact project plans and designs.
Clear communication and Coordinated effort:
- Foster transparent and continuous communication links that include the principals, owner, designer, project staff, subcontractors, and suppliers.
- It is crucial to ensure transparency and delineate the responsibilities, roles, and terms of engagement of the different parties involved in the work.
- Incorporate tools like project boards, apps, and other innovations to promote communication, document sharing, and collaboration tasks.
Consistency with Guidelines and Norms:
- Maintain a continued awareness of the legalities, guidelines, drafting requirements, and norms of the construction business that are appropriate to the project.
- Make sure that all the undertaking is taken care of within the legal and regulatory aspects to avoid extra costs, penalties, or any kind of legal problem.
costs
- Recognize and distinguish between the risks and problems incurred while undertaking the task as well as financial, ecological, and safety risks.
- Develop risk management techniques and emergency management procedures that will be able to address the risks and avert their immersion in the project by providing a course of action.
Quality Affirmation and Control:
- Accomplish strong quality inspection and control cycles so the value and materials can meet the nature of workmanship throughout the project.
- Lead normal reviews, testing, and audits quickly to try to improve the quality and standard of the project by identifying issues that may arise from wrong implementations or deviations from the project guidelines.
Resource Arranging and Management:
- Emphasize human resources selection, equipment & facilities, and manufacturing materials. Let these ventures have definite plans for initiation, implementation, and achievement.
- Examine the asset utilization rate and optimize it to boost efficiency or prevent overloads, deficits, or delays and make adjustments when needed.
Wellbeing and Safety Measures:
- Primarily, incorporate things to do with the well-being and security on the site by commandeering careful security plans, and strategies, and constructing health programs.
- Embark on regular mental well-being tests, assessments, and toolbox talk sessions geared towards creating a safety culture within workers.
Change Management:
- Emphasize the well-being and protection of the work crew during the construction of the building through the inculcation of effective security approaches, strategies, and provision of programs.
- Collaborate with the standard wellness assessments, risk investigations, and toolbox talks which in the end materialize a safety culture in the line of duty.
Provider and Subcontractor Management:
- Choose a reliable subcontractor and supplier that has a proven track record of delivering contact on time without exceeding the set budget.
- Enumerate the authoritative scale and responsibilities, and uphold open channels of communication with subcontractors, suppliers, or partners during the same period.
Continuous Improvement:
- Use input from each expedition to generate reviews and illuminations which can in turn be used to demonstrate where management methods, strategy, and operations can be improved.
Building up the remedial activities and best practices for these projects will bring about the rectification of issues and improved outcomes in future projects.
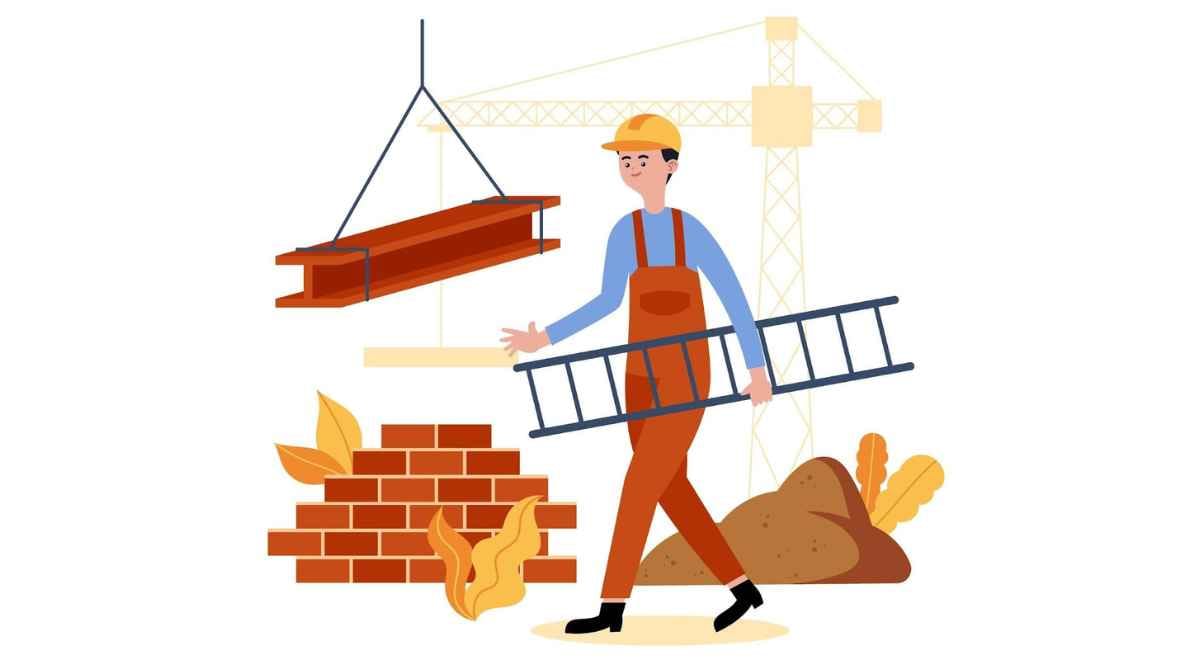
Conclusion:
The norms in the construction and renovation vary because of the errors in the structure and design. Teach yourselves to learn a lesson, which is you don't have to slap on aches by yourself; sometimes, losses are borrowed, just like a decade-long Arkansas land that proves to be integral to someone's well-being.
Finally, good communication, management of essential installations, and deliberate moves are the keys to avoiding construction mistakes and improving the overall quality. Moreover, documenting change or upgrade in the construction plan is another component of the topmost profound effect that incorporates it.
Comments ()